- Posts
- Renewable heat
Renewable Energy & Recovery: Focus on low-grade heat for industry
Hugues Defreville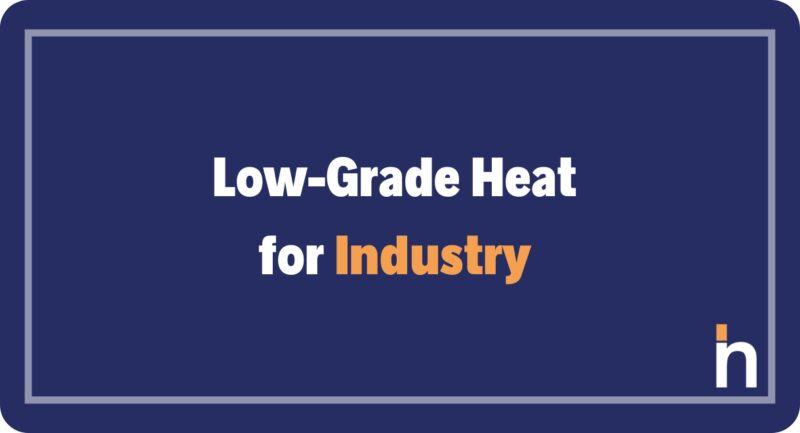
Introduction: Heat for Industry
Heat (or thermal energy) plays a crucial role in industrial processes, using different carriers (hot air, hot water, steam, oil, etc.) and different temperature ranges. In a previous article[1], we explored the major applications of heat, revealing that 30% of industrial heat requirement is for “low temperature” application below 100°C.
But what exactly lies behind the terms heat demand, process heat, and heat sources? Let’s explain.
Low Temperature applied to industry: What is it?
As we discussed in the article on renewable heat, heat is mostly produced directly by each industrial site to meet its specific requirement. These needs vary widely depending on the sector of activity due to different manufacturing processes that require different heat inputs: typically, low grade heat (below 100°C), medium grade heat (between 100°C and 400°C), and high grade heat (above 400°C). Various energy carriers are also used to transfer heat from the production source to the application: hot air, steam, hot water, thermal oil, etc. Moreover, even within the same industrial sector and type of production, heat requirement can differ depending on the chosen technologies, the age of the production line, etc.
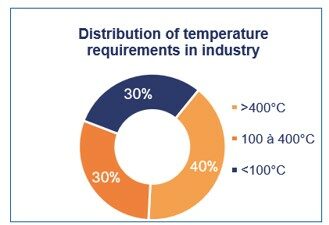
graph newheat
To illustrate these differences, let’s look at two typical processes found in the food industry:
- Thermal drying processes: These generally operate by direct contact of the material to be dried with hot air. In the food industry, thermal drying temperatures range from 30°C to 290°C, with the majority below 150°C (thus low temperature).
- Sterilization of ingredients: Typically performed at around 120°C by steam injection (medium temperature).
Key Takeaway: On a single industrial site, different processes often (if not systematically) require different heat inputs.
The term “low grade heat” (or low temperature) in industry therefore refers to all processes that require heat below 100°C.
Technical clarification: a process that requires a temperature higher than 100°C (for example 150°C) may include a significant proportion of heat requirements below 100°C. If we take the example of drying processes, most of the time these processes heat air at outside temperature up to a set temperature. Even if the heat required by the process is in the form of air heated to 150°C, some of it can be produced at low temperature (down to 100°C). This is known as pre-heating.
This is the type of technical solution we have implemented with the LACTOSOL plant at the Lactalis site in Verdun.
Next, we’ll find out why this distinction is necessary!
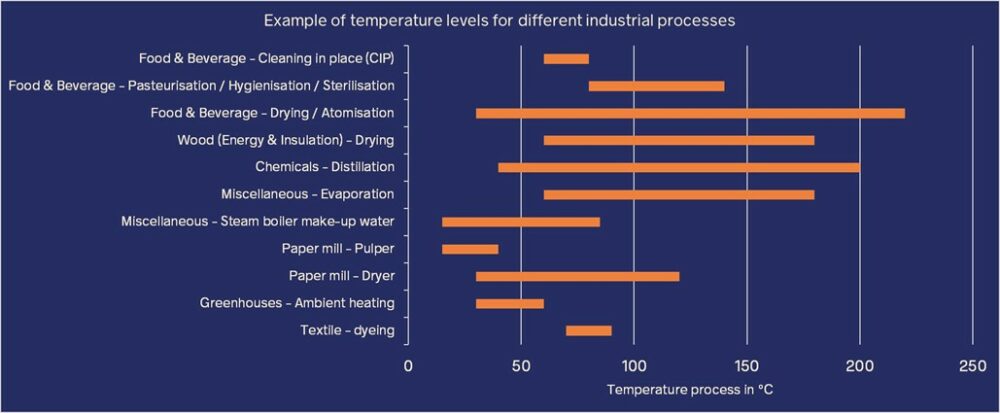
The challenge of renewable energy & recovery: managing temperatures
Temperature management with fossil fuels:
Historically, the ease of use and versatility of fossil fuels allowed industrial sites to pay little attention to this issue.
A gas or oil boiler works efficiently at both 50°C and 250°C. By designing the energy system to meet the needs of the most demanding consumer (highest temperature), the industrial site ensures it can supply each process with a single heat distribution network.
For example, on a food processing site requiring pasteurization (at 90°C with hot water), cooking (at 160°C in ovens with steam exchangers), and cleaning (at 62°C with hot water).
It is straightforward with a fossil-fueled boiler: simply produce steam at 180°C and supply each process. For cooking, send steam directly to the appropriate exchangers. For pasteurization and cleaning needing hot water, mix the steam with cold water to achieve the desired temperature.
Essentially, you produce 180°C steam to obtain 62°C hot water – a wasteful approach!
Temperature management for renewable energy & recovery:
This “management” of temperatures becomes a real challenge when integrating renewable energy and recovery (RE&R). Most renewable heat production sources, except those involving combustion, are less efficient at high temperatures. Their efficiency is inversely proportional to the target temperature: the higher the required temperature, the lower the efficiency (the ratio between incoming and outgoing energy). In the process heat field, 50% of waste heat sources are below 100°C, representing an energy volume of 60 TWh available for recovery.
Thus, finely adapting production to actual consumption needs is crucial. Furthermore, when replacing processes or building new plants, equipment choices should favor lower temperatures. Although these choices may involve higher upfront costs, they offer significant long-term economic and environmental benefits by maximizing the use of RE&R energy.
This requires a transformation in the energy systems of factories.
Instead of centralized, non-optimized energy production, the current trend is to supply each process with its target temperature to benefit from the decarbonization advantages of renewable and recovered heat sources.
RE&R Heat sources
Newheat’s scope of action covers all technologies for producing renewable and recovered heat.
Our objective is to decarbonize in a competitive and virtuous manner by combining the most environmentally friendly renewable energy sources (in terms of CO2, biodiversity, resource availability) while adapting to local constraints and following a prioritization model:
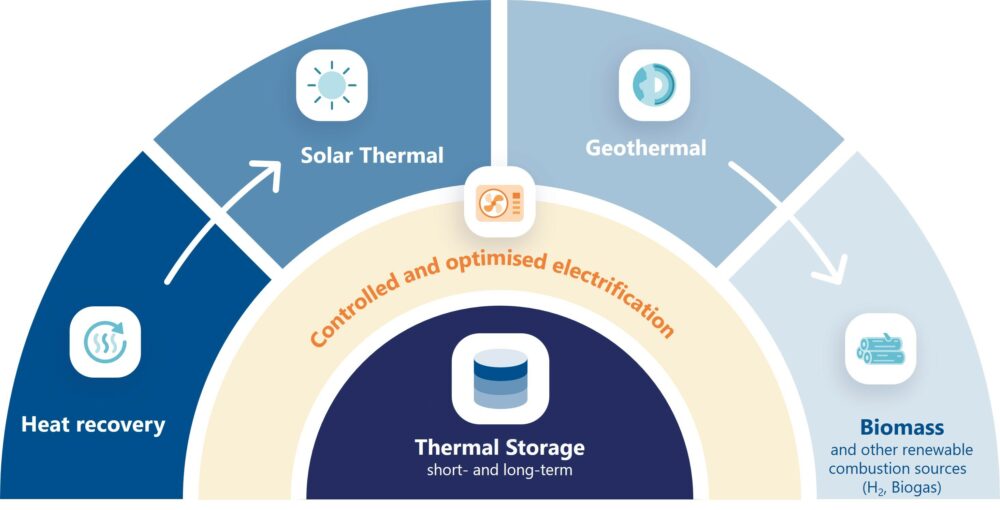
Newheat’s merit order
Here is an overview of these energies:
- Waste Heat Recovery: This involves the valorization of the heat that is inevitably released and lost during an industrial process. The temperature of recovered heat varies widely depending on the processes and sources, from high-temperature fumes (above 300°C) to low-temperature flows like heat generated by refrigeration
- Solar Thermal[2]: Numerous solar thermal technologies produce heat at different temperature ranges. Generally, the hotter it is, the more expensive it becomes.
- Geothermal: This involves extracting heat from underground to use it on the surface. Different types of geothermal energy exist depending on the depth of the heat source and soil characteristics.
- Combustion of Renewable Resources: This could involve biomass (with ensured local and sustainable supply) or biogas.
These production means can be combined with electrification solutions such as
- Heat Pumps (HP): This technology allows temperature levels to be increased using electricity efficiently. The efficiency of this technology is also highly dependent on temperatures, with newer HPs capable of reaching up to 120°C, and some manufacturers even announcing upcoming models that can reach up to 150°C.
Finally, all these technical solutions and their potential combinations are centered around
- Thermal storage systems[3], which provide flexibility and robustness to the energy system between producers and consumers.
There are also different technologies for these storage solutions, depending on the different temperature ranges, but there is a real “market” in terms of technology and economic competitiveness for solutions that can store heat above 100°C, the temperature above which water can no longer be used as a storage material.
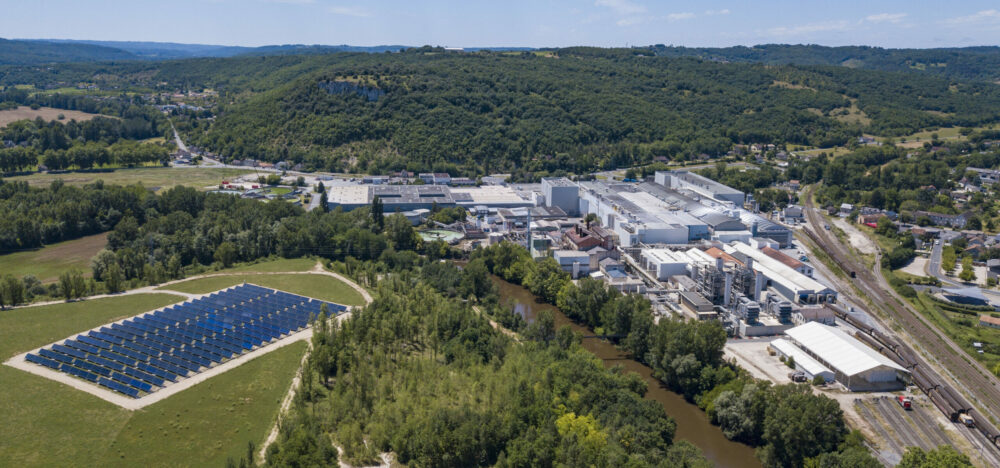
The CONDATSOL solar thermal plant supplies heat to the Condat paper mills
Discover Low-temperature renewable heat solutions that are already effective for industry
Here are three examples of Newheat’s renewable heat plants on industrial sites:
If you want to supply your industrial site with decarbonized low-grade heat, contact our team of experts dedicated to industrial solutions!