- Posts
- Industrie
Waste Heat: The First Resource to Exploit for Renewable and Sustainable Heat
Hugues Defreville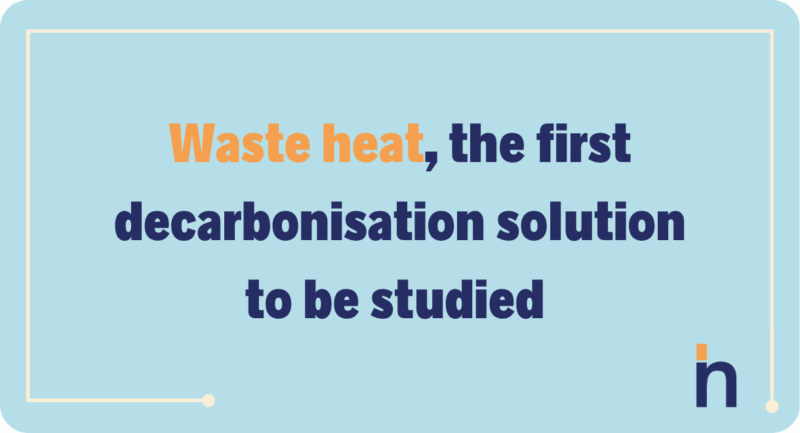
The decarbonisation challenges of industries and district heating networks (DHN)
The decarbonisation of industry and district heating networks is at the heart of strategies to combat climate change, both in France and worldwide. Industry currently account for around 20% of greenhouse gas (GHG) emissions in France, while at the European level, this figure reaches almost 25%. Faced with these challenges, the need to reduce these emissions is becoming crucial. In 2022, global CO2 emissions crossed the alarming threshold of 36.4 billion tonnes, highlighting the urgency of taking concrete action. The costs of inaction are estimated at several trillion euros, while the growing dependence on fossil fuels exposes industries and communities to price fluctuations and energy instability. To address these major issues, the transition to sustainable and efficient low-carbon heating solutions is essential as it allows reducing the carbon footprint and ensures a sustainable energy future.
ADEME ‘s EnR’CHOIX
In order to guide the energy choices of industries and local authorities in their decarbonisation objectives, the ADEME Heat Fund has been using a “decision tree” called “EnR’CHOIX ” since 2024.
Firstly, ADEME recommends reducing energy consumption through energy-saving and energy-efficiency measures. Then, it prescribes to mutualise the needs and means of heat production and distribution. To do this, it is advised to connect or create new networks based on a mix with more than 50% renewable and recovered energy (RE&R). Finally, ADEME recommends optimising and prioritising the use of RE&R.
Before considering the creation of renewable energy systems that cannot be relocated (i.e. that are available in the immediate vicinity of the place of consumption, such as solar thermal or geothermal energy) or that can be relocated (biomass, for example, which can be transported from its place of production to the site where it is needed), priority should be given to the use of an energy that cannot be relocated and that already exists: the recovery of waste heat.
ADEME specifies that access to aid depends on compliance with this decision tree, and that the beneficiary must justify the solutions chosen according to these stages.
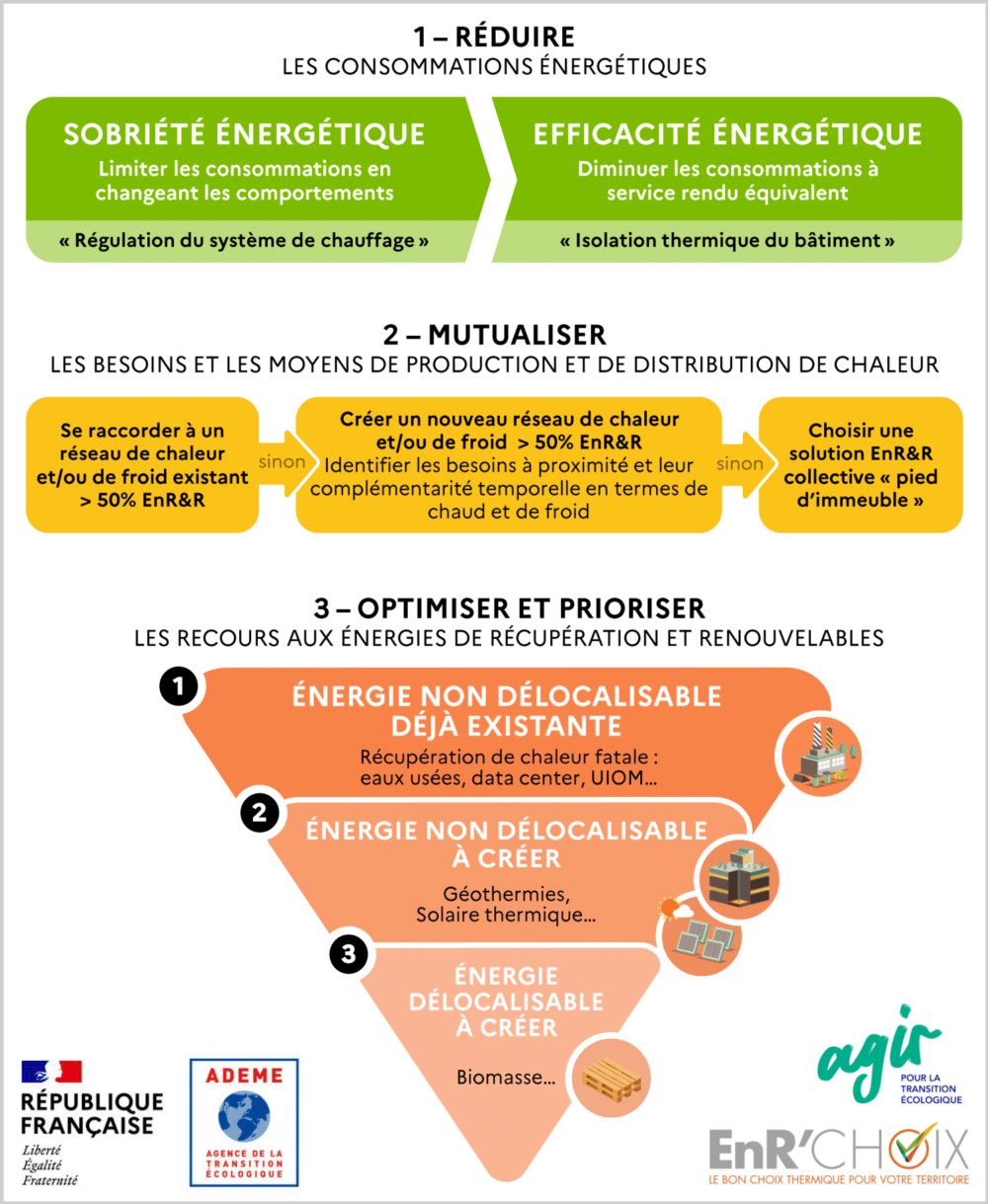
EnR’Choix – Decision tree determining the obtaining of ADEME subsidies
In a previous article, we identified waste heat as being part of the large family of renewable energy sources, in relation to the low-temperature needs of industry.
But what’s behind the term ‘waste heat’, where is it found and what’s the point of recovering it? Let’s dig into it in this article!
What is waste heat?
What is it about?
A large amount of heat is generated on industrial sites, either directly to power various production and transformation processes, or indirectly to produce refrigeration. However, a significant proportion of this heat is not used. Waste heat is that which is rejected into the environment (into the air or water, for example). Although this energy is often lost, it can be recovered and reused. In fact, via various vectors such as hot air, steam or hot water, it can ‘still’ be used to heat industrial processes, buildings or even to produce electricity. This solution enables industries and DHNs to reduce their environmental impact. It is also known as recovered heat.
Where is it found?
Recovered heat can come from industries, electricity production sites, wastewater treatment plants (WWTPs), waste treatment plants such as household waste incineration plants (UIOMs), or data centers.
What is the potential in France?
In France, the potential for waste heat is estimated at more than 100 TWh, according to a study carried out by ADEME in 2017. Given that final energy consumption by industry is estimated at more than 300 TWh/year, this means that around 1/3 of the energy used by industry is ‘lost’.
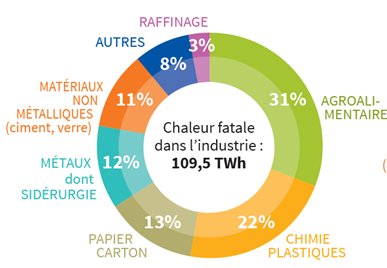
Waste heat in industry in 2015 – ADEME, 2017
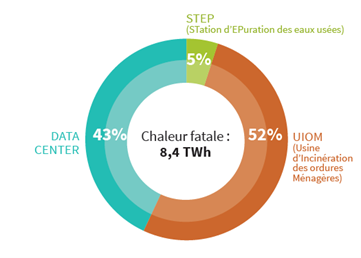
Waste heat in STEPs, IUOMs and Data Centres in 2015. – ADEME, 2017
It is important to note that not all sources of recovered heat are used in the same way, and it is necessary to reason and prioritise by temperature level in order to make the most of their potential.
To put it simply, half of the deposits are below 100°C and the other half are above 100°C.
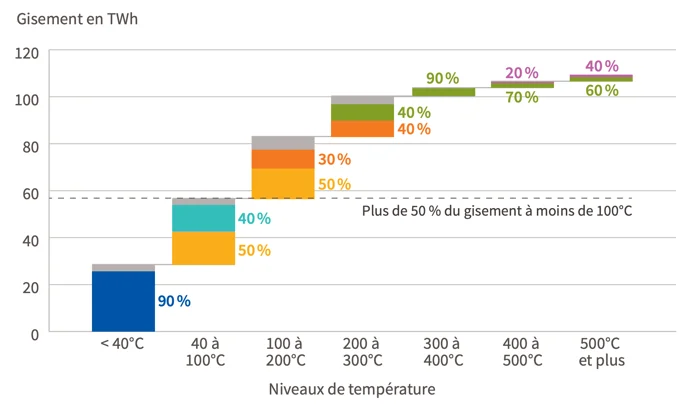
Waste heat deposit by temperature level – ADEME, 2017
To summarise, recovering and making the most of this waste heat, which accounts for a significant proportion of industrial energy consumption, is a major challenge for the decarbonisation of industry and district heating networks.
How can this heat be recovered and used?
How to recover it ?
Where does industrial waste heat come from? It can be found in:
- The cooling of industrial processes or equipment: for example, on refrigeration units used to produce cold to keep dairy products cool;
- Moist air evacuated by a dryer: this is the case in a drying tower used to transform condensed milk into milk powder. The moist air leaving this tower contains a large amount of heat recovery;
- Fumes from a boiler or kiln: for example, fumes from a glass furnace.
There are also other more diffuse sources that need to be identified. Whatever they are, it is important to consider their specific characteristics: calorific intensity, type of emissions, or the need to integrate a cleaning system to prevent clogging. The aim is to maximise energy performance while ensuring that using this source has no impact on the process.
It is also necessary to look ahead to the future use of the source of waste heat, so as not to use a source from a process that is set to disappear or from a fossil heat source (recovery from gas boiler flue gases, for example).
How can it be used?
Once this heat has been recovered, there are several ways of using it:
On site or to go?
The first thing to do is to use this waste heat on the site where it is recovered:
- Either as self-consumption within the same equipment, by recovering the heat from the fumes of a kiln and using it to preheat the products entering the same kiln, for example.
- Or within another piece of equipment or another process, by recovering heat from kiln fumes to preheat the drying air in an upstream dryer.
Sometimes a site has a surplus of waste heat, meaning that it has more to recover than it needs at these temperature levels. In such cases, Newheat investigates the proximity of other industries that might have an equivalent need, or a nearby district heating network that we could connect to, so that end users can benefit from low-carbon, competitive heat.
Direct use or temperature recovery?
If the temperature of the heat source is high enough, it can be reused directly on another piece of equipment, another process or another nearby site. This is known as direct use.
On the other hand, if the temperature is not high enough to be used directly, it will be necessary to use equipment, such as a heat pump, to raise the temperature, at a cost in terms of electricity consumption.
In this way, it is essential to adopt a territory-wide approach, rather than limiting oneself to a single site. In some cases, it may be economically more advantageous to recover waste heat from a neighbouring site or district heating network. Where temperature levels are compatible, this solution avoids the need to install thermal enhancement equipment (which is costly and consumes electricity), while optimising existing processes.
When studying a global solution, we prioritise sources according to the heat levels of the needs to be covered: we first seek to address the needs from waste heat deposits at the same level, in order to avoid unnecessary electrification. Then, if there is a low-temperature source left, we can use a heat pump to raise the level to meet higher heat requirements.
Calories or electrons?
When we talk about recovering waste heat, we generally mean recovering this energy to meet the thermal needs of the plant itself, other neighbouring companies or a nearby district heating network. However, this waste heat can also be used to produce electricity under certain conditions. This is the principle of the organic Rankine cycle (ORC) machine. This electricity can then be used on site, for self-consumption, or fed into the electricity grid. However, converting heat into electricity is less efficient than converting it directly into heat, particularly at low temperatures, where the efficiency of conversion into electricity is below 10%.
Consequently, this solution should be reserved for situations where all the potential thermal uses of the recovered heat have already been exploited within the site or nearby. It is therefore an option of last resort for recovering residual waste that has no other outlet.
In short, there are several ways of exploiting waste heat. As each industrial site has its own unique characteristics and constraints, it is essential to adopt a global approach across the entire region. This enables heat sources and heat sinks to be accurately identified, the economic balance of different solutions to be assessed, and the use of available waste heat to be maximised to achieve the best results.
Why is waste heat recovery the first decarbonisation solution to be studied?
A reminder of Newheat’s use prioritisation model
At Newheat, assessing the potential for waste heat is the first step in our thinking when helping an industrial site to decarbonise its heating needs. As in the case of solar thermal energy, our approach is based on an analysis of the operation and temperature levels of each process in order to characterise the match between sources and sinks of waste heat. This assessment enables us to identify whether there is a need to use other complementary RE sources (solar thermal, geothermal, biomass and other renewable combustion sources), to determine if there is a need for electrification and to choose the type of thermal storage required.
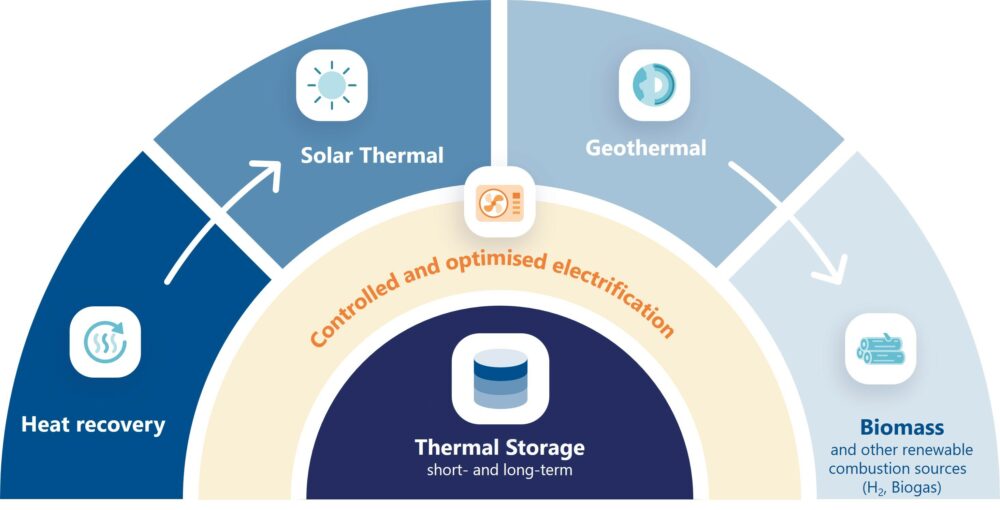
Newheat’s prioritisation of renewable heat technologies
Why do we say that it is the “1st layer”?
Recovered heat is distinguished from other renewable heat sources, such as solar thermal, biomass or geothermal, by its ability to make use of a resource that is already available and recoverable. There are several ways in which this can be achieved:
- From an economic point of view: recovering waste heat is often one of the most economical ways of decarbonising processes. It makes the most of a source that is already available locally, and benefits from various aid mechanisms, such as ADEME’s Heat Fund, Energy Savings Certificates (CEE) and local subsidies. These schemes boost its competitiveness, even when the price of fossil fuels such as gas, fuel oil or coal is low. This enables industries to make substantial savings on their long-term energy costs, while reducing their carbon footprint.
- From an environmental point of view: recovering waste heat and using it to replace fossil fuels helps to reduce greenhouse gas emissions from industrial sites. The environmental impact of this type of solution remains limited, because the amount of equipment to be installed is small, requires little land and does not consume resources such as biomass. Additionally, the system does not generate particles from the combustion of raw materials.
- From a time perspective: the implementation of recovery projects is often quicker than that of other solutions, because they require little or no land and require fewer administrative authorisations.
In short, a waste heat recovery project can quickly and cost-effectively reduce a site’s greenhouse gas emissions.
Concretely, how does it work?
Let’s take a concrete example of a factory producing clay roof tiles where Newheat has installed a waste heat recovery system.
First of all, let’s explain how this type of plant works:
- The first stage consists of extracting the clay, the raw material, from the quarries, then transporting it to the factory where it is crushed, kneaded and moistened to obtain a homogenous paste, ready to be shaped. This paste is then moulded into the desired tile shape, according to the specific requirements of the factory.
- Once the tile has been shaped, it goes through a drying stage: the water must be largely removed from the tile so that it does not explode during firing. This drying, which is carried out using hot air generally between 70°C and 160°C, requires a lot of heat, often supplied by gas and the recovery of waste heat directly from the kiln.
- The dried tile is then fired for several hours in a kiln at around 1000°C! It is at this stage that the clay becomes hard and takes on its final shape. Most of this process is also carried out by burning gas. The fumes coming out of the chimney of this kiln are generally at temperatures in excess of 100°C.
- Finally, the tile is ready to be packaged and marketed.
Key figures (reduction in dryer gas consumption, CO2 saved)
As we have described, it is the drying and firing stages that require a lot of heat. The project carried out by Newheat for this customer involved recovering heat from the kiln fumes and other sources of waste heat from the kiln in order to eliminate 80% of the kiln’s natural gas consumption. In terms of the site’s total consumption, almost 10,000 MWh PCS will not be consumed, or around 2,100 tCO2/year avoided.
From an economic point of view, and with current gas prices, this type of project pays for itself in less than 5 years. In years when gas prices rise sharply, as they did during the energy crisis of 2022/2023, the payback time will be even shorter.
Newheat added value: integration of a thermal storage tank
This rate of reduction in gas consumption would not have been possible without the 1,500 m3 storage tank, which enables heat to be recovered from the kiln at weekends, even when the dryer is shut down! Newheat provides real added value: our engineering and modelling teams have developed considerable expertise in modelling thermal storage systems, which are particularly well suited to recovering waste heat. Read our article on this solution for more details.
Heat pump to raise the temperature
It should be noted that the temperature at the heat recovery point was higher than that required for the dryer. It was therefore not necessary to use a heat pump. In fact, we prioritised by thermal level and found that the deposits available did not require electrification, which limited the operating costs of our solution. This type of solution is nevertheless offered by Newheat, in order to adapt to the specific features of each process, in particular to make the most of the heat present in the moist air leaving the dryer.
Find out more about our other projects and installations tailored to our customers’ needs on our dedicated page.
To conclude
Waste heat recovery is an essential solution in the quest to decarbonise industrial sectors and district heating networks. By making the most of a resource that is often neglected, and without impacting the operation of the industrial site, this approach not only makes it possible to significantly reduce greenhouse gas emissions, but also to optimise industrial energy costs. Thanks to their rapid implementation and administrative simplicity, recovery projects offer a cost-effective alternative to today’s energy challenges.
By incorporating this approach into their decarbonisation plans, industries can not only meet the regulatory requirements that are set to increase over the coming years, but also respond to the growing demands of their customers. They can then differentiate themselves from their competitors and play an active role in the fight against climate change.
It should be noted that there are not always sufficient sources of waste heat or heat available at all temperature levels to cover all the needs to be decarbonised. That’s why Newheat offers other solutions.
Recovering waste heat can then be supplemented by solar thermal and/or geothermal energy to harness abundant, local, input-free energy. Electrification, measured and optimised using heat pumps and/or electric boilers, can also be added depending on the needs of the site. And finally, the use of renewable combustion sources, using biomass boilers for example, can decarbonise heating requirements at higher temperatures.
Whatever the customer’s needs, Newheat is committed to preserving and making the most of local energy resources to provide a tailor-made solution.
After reading this article, are you convinced of the benefits of recovering waste heat on your industrial site and would like to study these solutions in more detail? Don’t hesitate to contact us for a chat!